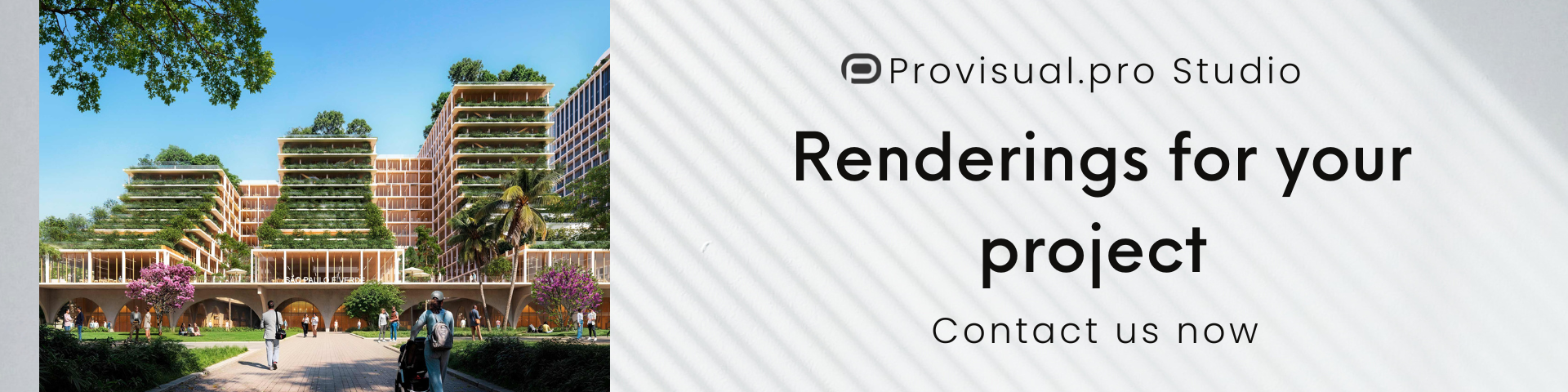
Think of the last thing you 3D printed, or even just the most recent object you used. Chances are it had some moving parts, or at least parts joined together from separately made pieces. From my computer mouse to my space heater, most of the manufactured items on and around my desk (and the desk itself) have connecting pieces. Sure, none of these things were made on a 3D printer, but as they’re put together now… well, they couldn’t have been.
The reason why is pretty small, but immediately recognizable: metal threads.
3D printed pieces are used frequently in prototyping, which leads to experimental opportunities for product design and assembly. The team over at Formlabs has had plenty of experience designing, tweaking, and redesigning prototypes to be 3D printed on their Form 1+. A common solution to connecting components of 3D printed models is the character key, a sort of male-female connecting piece assembly. Check it out in action:
That’s a pretty clever construction method, but it isn’t very realistic to use in something that might need to be connected, unconnected, and reconnected repeatedly. Many traditionally manufactured pieces utilize metal threads for their effectiveness in secure connections and ability to be repeatedly used. Makers have been looking for ways to work metal threading into 3D printed pieces for some time. And now, after some trial and error, the Formlabs team has come up with some options. It has ranked them, for convenience, starting with the most effective method and going down to the least effective.
- Print a pocket for metal threads (add a nut).
- Print threads and chase with a tap.
- Use thread-cutting screws designed for plastics.
It also notes (emphasis is Formlabs):
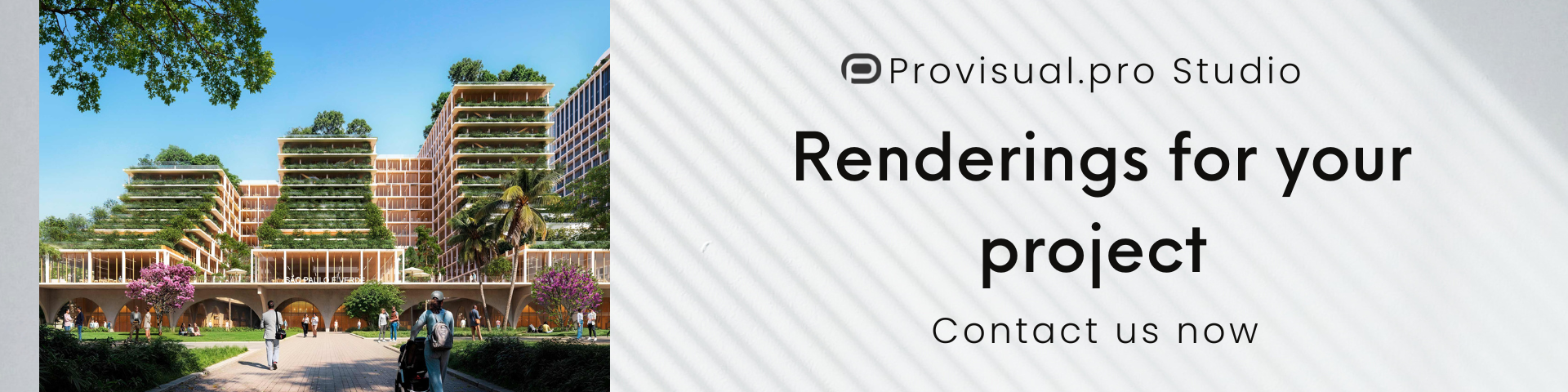
“AVOID using press-fit or heat set threaded inserts! Even if they are designed for ‘plastic,’ they do not work well in our acrylate photopolymer resins.”
Of course, they go into more detail about methods and findings in their Inside Formlabs blog post.
The Formlabs team has tested these techniques thoroughly. Note that with male and female thread sizes, 1⁄4-20 or larger have the best chance to form functional parts without necessitating post processing, and smaller screws tend to require more customization for better fastening. “For example,” it notes, “printing a semi-circular thread profile (on screw and nut) and using a 0.1 mm offset gives better thread engagement with improved wear characteristics.”
Formlabs offers an STL download for its most successful test so you can try it at home. It also recommends ordering steel hex nuts, coupling nuts, and forming screws from McMaster.
Will you try one of these methods? How did it work for you? Let us know what your thoughts on the process are in the 3D Printed with Screw Threads forum at 3DPB.com.
When it comes to 3D real estate visualization in the USA, our service provides the perfect solution for bringing property listings to life. Through our platform, you can easily access cutting-edge 3D renderings that showcase your real estate projects in a way that attracts potential buyers and investors. Whether it's residential, commercial, or mixed-use properties, our team of experts uses advanced technology to create immersive visualizations that highlight the best features of your property, making it easier for clients to imagine the space as their own.
Through our website, you can quickly get high-quality 3D real estate visualizations that are tailored to your specific needs. With our help, you'll stand out in the competitive real estate market by offering potential buyers a realistic, interactive view of your property. Our efficient process ensures a fast turnaround time, while our attention to detail guarantees that every aspect of the property is represented accurately, giving you a powerful marketing tool to promote your real estate listings.