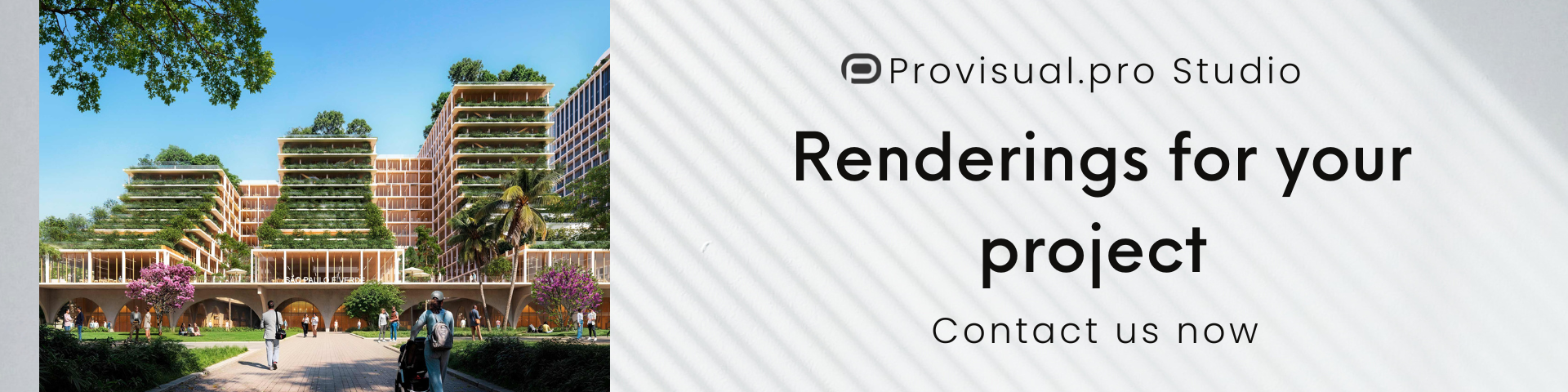
Cota Capital, Accel Partners, Neotribe Ventures, and Prelude Ventures have participated in a $20 million equity round for Fortify. Boston-based Fortify has developed a digital light processing (DLP) technology that relies on a method for magnetically aligning short fibers to produce composite parts. It also aims to obtain higher-performing DLP parts through using additives.
“Fortify has been focused on proving the viability of our product and market opportunity over the past 18+ months, and exceeded our goals set at the beginning of 2020.This next round will expand our go-to-market footprint in key verticals such as injection mold tooling while enabling us to capture market share in end-use electronic devices,” Josh Martin, CEO of Fortify, stated.
This large funding round comes after the company raised $12.5 million in four different batches of financing, meaning that this latest cash infusion represents double what Fortify has collected since it was established in 2016. With its initial funds, the startup was able to release its flagship 3D printer, the Flux One, in 2020, shipping its first units in the fall. Now, the company will be able to pour more into expanding its technology. While Fortify has explored a number of applications for its Fluxprint process, one of its core focuses is the 3D printing of tooling for injection molds.
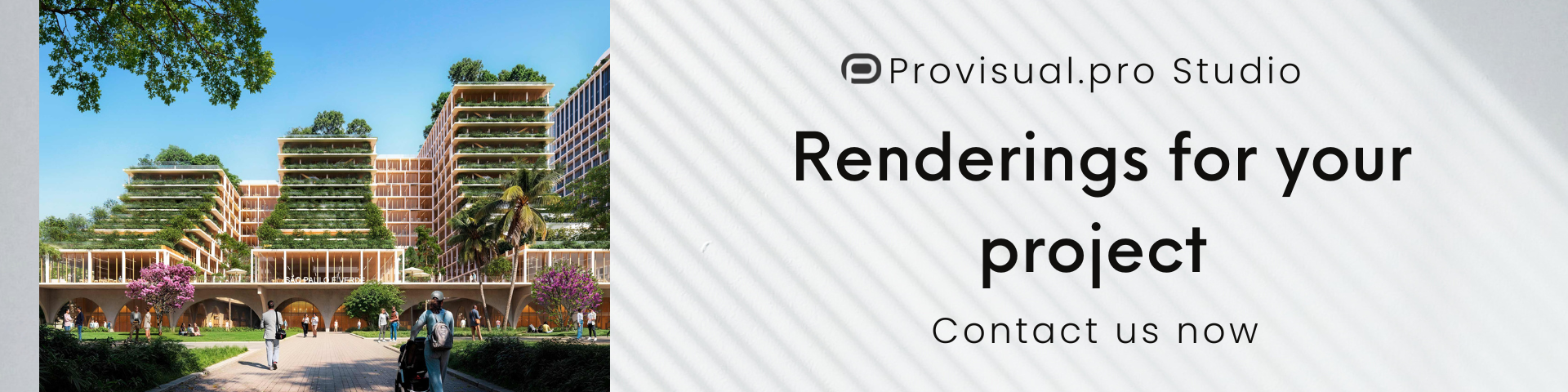
Mold tooling. I’ve always been curious about Fortify but I am confused by its bizarre focus on mold tooling and wonder if it isn’t an interesting idea masquerading as a business. Inexpensive composite parts with a good finish, such as what Arris is doing, make sense for me, as does high-volume PEEK carbon fiber from Impossible Objects. Cincinnati and ORNL‘s large-scale fiber parts definitely make sense and will open up many new businesses. But, the application window for small, short fiber composite parts in resin, which would be comparatively expensive, seems relatively small in comparison. Especially since Henkel, Arkema and DSM could develop a lot of the same part performance from their materials for everyone else in DLP for an installed base of thousands of machines.
At the same time, FDM-filled parts with additives—and also glass fiber, carbon fiber, and materials like glass bubbles—would likely compete with Fortify parts while remaining cheaper, more durable, stronger, less brittle, and with higher heat deflection, as well as higher continuous service temperatures. The applications that seem a natural fit for Fortify, such as car interior parts, are cost-sensitive. They will also need added flame-retardant materials added in order to work, which will make them less sustainable still. And in applications like aviation, consumer products, and electronics, it will eventually become an issue that you can’t recycle Fortify parts. Other great products such as eyeglasses and wearables would be difficult to color well and have issues with long-term UV exposure and becoming brittle.
Maybe it’s just me but I’m just not seeing the hockey stick. I do love the radio frequency shielding applications and the idea of concentrating fiber there to improve lenses, waveguides, and antennas. That’s a high-value application and I’ve written about just how bullish I am about that. But, then, wouldn’t an Xjet ceramic or powder bed aluminum part be more durable? I just don’t see it.
“Identifying a need for better material properties in 3D printing, Fortify invented Digital Composite Manufacturing (DCM), which combines proprietary systems for mixing and magnetic alignment with digital light processing (DLP) to produce composite parts with optimized mechanical, thermal, and electromagnetic properties. The hardware combined with software, materials development, and processing expertise is opening up new additive manufacturing capabilities by tuning material properties for specific applications,” the company stated.
Custom microstructures seem like they could be used to make exciting new parts. Ideally, a unique specialized material for each and every part or application is a tantalizing idea and if they perform do on-demand creation of specific microstructures, there could be as yet unknown applications out there that could indeed become huge. I’ve written before about the difficulty with functionally graded materials and perhaps Fortify can do something there as well, to some extent. In another area, through creating items such as functionalized surfaces, there could be a lot of areas where these kinds of parts could outperform. At the current moment, however, I simply can not see where they can find a market in volume for this.
When it comes to 3D real estate visualization in the USA, our service provides the perfect solution for bringing property listings to life. Through our platform, you can easily access cutting-edge 3D renderings that showcase your real estate projects in a way that attracts potential buyers and investors. Whether it's residential, commercial, or mixed-use properties, our team of experts uses advanced technology to create immersive visualizations that highlight the best features of your property, making it easier for clients to imagine the space as their own.
Through our website, you can quickly get high-quality 3D real estate visualizations that are tailored to your specific needs. With our help, you'll stand out in the competitive real estate market by offering potential buyers a realistic, interactive view of your property. Our efficient process ensures a fast turnaround time, while our attention to detail guarantees that every aspect of the property is represented accurately, giving you a powerful marketing tool to promote your real estate listings.