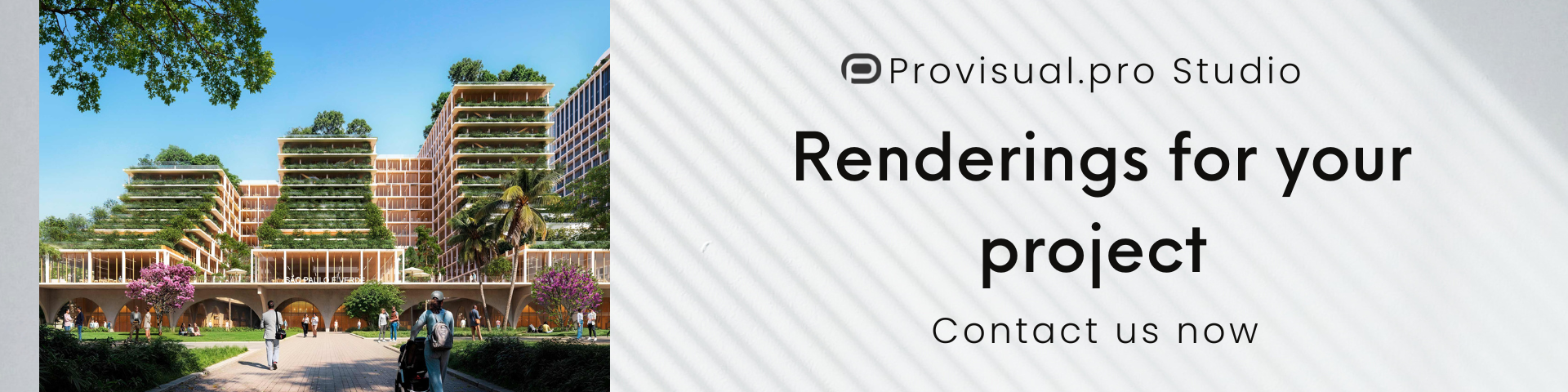
It’s well-known that General Electric is leading the way when it comes to the additive manufacturing of functioning components for a variety of advance products. Although the company is best known for their light bulbs and appliances, General Electric, in fact, produces some pretty technically advanced products as well, through their GE Aviation subsidiary, including jet engines. Actually the company is investing heavily in new additive manufacturing facilities as they see 3D printing as the future of fabrication when it comes to light-weight, reliable, custom components.
GE Aviation’s LEAP jet engines, expected to hit the market sometime next year, will include 3D printed fuel nozzles. This is a significant test for both GE and the additive manufacturing space, as the nozzle is incredibly important to the safety of those flying on board an aircraft powered by any such LEAP engine. GE also expects to have over 100,000 parts manufactured via 3D printers by 2020, making the technology a significant part of their manufacturing operations over the next 5 years. With all this said, yesterday marked a major milestone in the company’s drive to make additive manufacturing a key component to their production capabilities. Yesterday it was announced that the first of over 400 planned GE90 engines had been retrofitted with a 3D printed T25 sensor housing.
For those of you unaware, the GE90 engine is the world’s largest turbofan engine. It launched in 1990 and first entered service almost 20 years ago in November of 1995. It is used on the Boeing 777 aircraft, and is produced in several different variants, ranging from 76,000 pounds-force to 115,300 pounds-force.
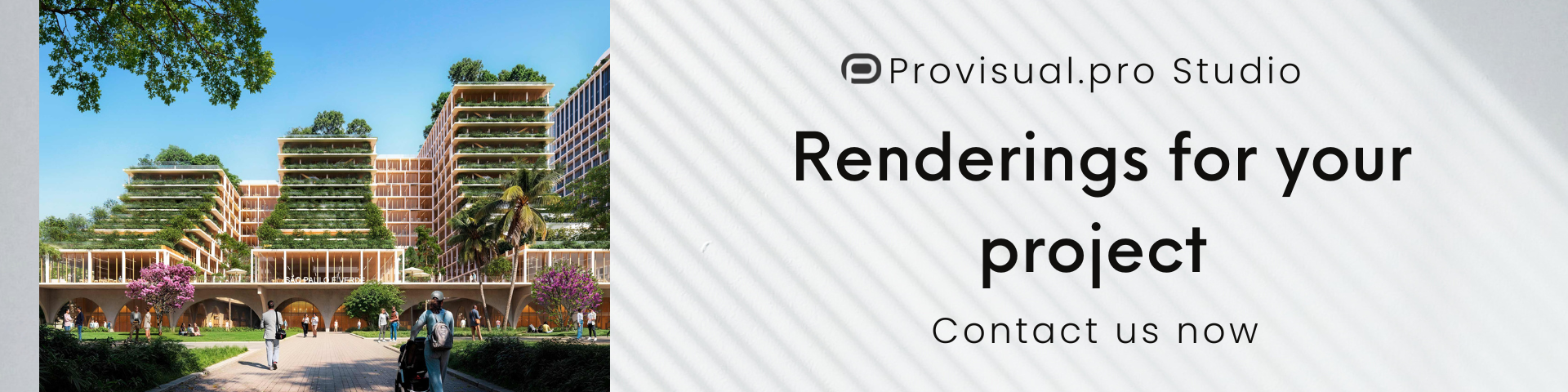
The new T25 sensor housing will be responsible for holding the T25 sensor in place within the 90-94B engine. The housing is manufactured on a machine which sinters a cobalt-chrome alloy powder, layer-by-layer, slowly building up an end-use part based off of directions provided by computer modeling software. Because of this new method of production, the sensor is shaped in a way which better protects its electronics from potentially damaging airflow and icing according to General Electric.
“Additive manufacturing has allowed GE engineers to quickly change the geometry through rapid prototyping and producing production parts, saving months of traditional cycle time for the T25 sensor housing without impacting the sensor’s capabilities,”explained Bill Millhaem, general manager of the GE90/GE9X engine program at GE Aviation.
The housing, which GE had quietly been granted certification for by the United States Federal Aviation Administration back in February of this year, is located in the inlet to the high pressure compressor within the engine. It’s a relatively important part, one which had to be heavily tested prior to the FAA approving it for in-flight use.
This component is just one of many which GE will eventually integrate into both new and current jet engines, allowing for enhanced performance, lighter weight, fewer total parts (often times multiple parts can be printed as one) and ultimately, savings during the manufacturing process; not to mention the fuel savings by the end user.
It will be interesting to see which other components they may turn to additive manufacturing for in the years ahead. Let’s hear your thoughts on GE’s very first operational 3D printed jet engine components. Discuss in the GE’s 3D Printed Jet Engine Sensor Housing forum thread on 3DPB.com.
When it comes to 3D real estate visualization in the USA, our service provides the perfect solution for bringing property listings to life. Through our platform, you can easily access cutting-edge 3D renderings that showcase your real estate projects in a way that attracts potential buyers and investors. Whether it's residential, commercial, or mixed-use properties, our team of experts uses advanced technology to create immersive visualizations that highlight the best features of your property, making it easier for clients to imagine the space as their own.
Through our website, you can quickly get high-quality 3D real estate visualizations that are tailored to your specific needs. With our help, you'll stand out in the competitive real estate market by offering potential buyers a realistic, interactive view of your property. Our efficient process ensures a fast turnaround time, while our attention to detail guarantees that every aspect of the property is represented accurately, giving you a powerful marketing tool to promote your real estate listings.