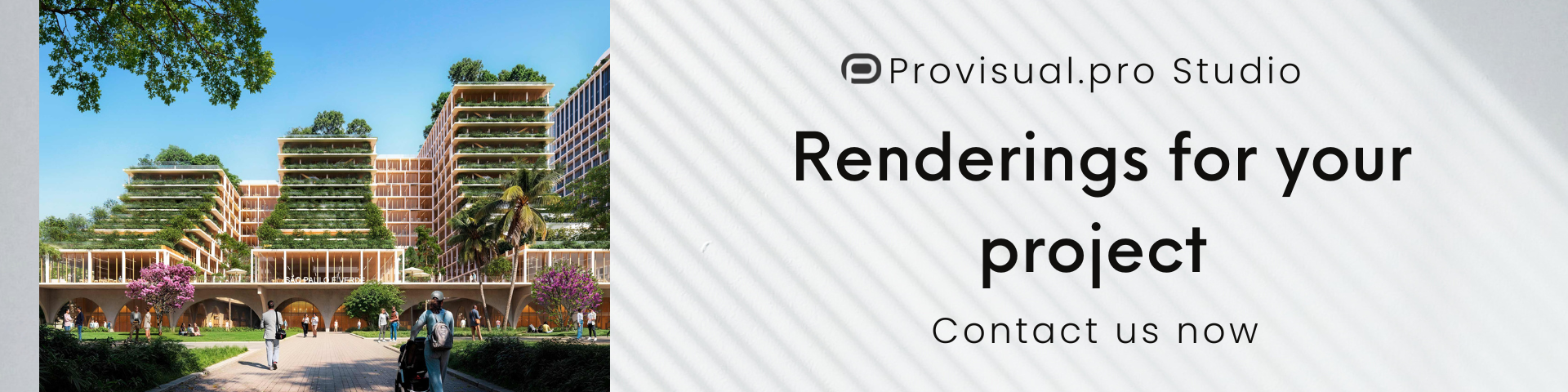
Thomas Sanladerer offers a variety of videos on YouTube regarding 3D Printing and parts. His build guides. tutorials, tips and basics center around the open-source RepRap family of 3D printers. In “The Materials Strength Test” Sanladerer demonstrates the strengths of four samples, with their specifications listed:
- Formlabs SLA sample: Formlabs Form1+, Formlabs white resin, 100µm layers
- ABS sample: Mendel90 w/ E3Dv6, 250°C, 60mm/s, far-east black, Slic3r and 200µm layers
- PLA: Printrbot Simple Metal w/ UBIS hotend, 208°C, 40mm/s, Printrbot purple sample PLA, Cura and 200µm layers
- Taulman Bridge: Nylon: Mendel90 w/ E3Dv6, 250°C, 50mm/s,Slic3r and 200µm layer
With entertaining dialogue, and some level of amusement on his part during the “semi-scientific experiments,” he examines the quality for each part in his video. His method is basically to “torture” the parts, seeing how they hold up—with nothing standing at the end—and I think even he nearly has his eye put out at one point in the process.
Material Quality
Sanladerer takes a preliminary moment to examine the cosmetic qualities produced by each of the processes used in printing the parts.
- Beginning with Formlabs, he points out that it feels very strong, He states that the SLA sample looks great overall and felt very strong in the hand. He notes that it has great detail, great reproduction, the overhangs look pretty good, and the sample just has great quality overall.
- The ABS part, which he points out is like a cheap part made in China, is pretty disappointing. The font isn’t very readable on the body of the sample, and the logo didn’t come out very well, due to inferior slicing. Looking pretty abysmal overall, the overhangs on the bottom are inferior. Sanladerer gives it poor presentation overall.
- The next part from is the Printrbot PLA sample produced on The Simple Metal and sliced in Cura. The fonts are fairly illegible but the overall print quality of the sample is good. The slicing turned out nicely, and overall the sample is “good.”
- The semi-glossy sample from Taulman Bridge turned out nicely, with an easy print nylon co-polymer that is a bit stringier due to softer filament. The production quality and detail is sharp, and Sanladerer points out how well nylon handles overhangs with no strings visible and it being as close to perfect as possible. His take on this sample is that it looks great.
The Breaking Test (manual)
And now for the fun part! Sanladerer begins the first torture test, explaining that this is a subjective test, trying to break the samples by hand, which is not an altogether pleasant experience for him with the first couple of samples. Sporting red, chafed hands, he points out that the samples were strong enough, except for ABS and Taulman Bridge.
- In testing the FormLabs SLA part, he simply was not able to break off anything with his fingertips.
- The PLA Printrbot sample, with the “same procedure, same fingers used” yielded the same results as the first sample, as he could not break off anything with his hands.
- With the ABS part, Sanladerer was able to break off pieces easily with his fingertips from the overhang, using no significant force. This was not a surprise to him, considering the ABS part is so cheaply made.
- Testing the Taulman Bridge sample, overhang pieces tore off easily instead of snapping off, being easily removed almost like tearing cloth, due to the nylon properties.
The Tension Test
In the next experiment, Sanladerer used clamps, a vice, and a weighted system (a bucket of water) to try and tear apart the pieces. Using a length of Spectraline to form hooks around the vice-encased samples to make sure he was pulling straight down on the part, he placed each sample in the vice, stressing it with tension from the weighted bucket as he filled it with water.
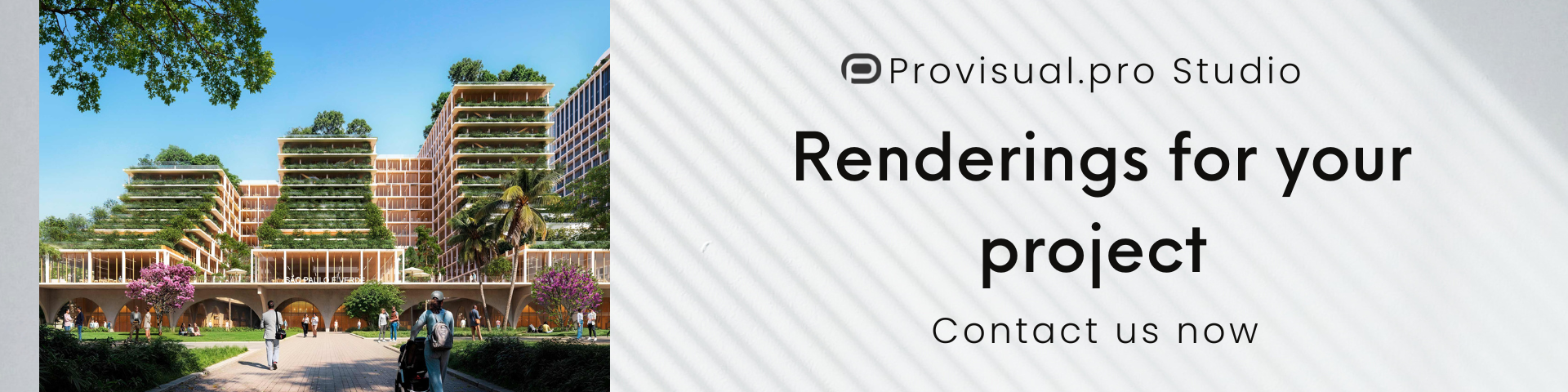
- The Formlabs sample did not fail until the water bucket was filled completely to the top, with Sanladerer lifting and lowering. This was with a bucket of water weighing close to forty pounds. While it took some amount of the time, for the piece to break, in the end it definitely did not “fail gracefully.”
- The ABS sample failed miserable and quickly. As he pointed out, it was the only sample that really failed this round.
- The PLA Printrbot sample was very similar to the Formlabs piece, but took a bit more force to snap.
- The Taulman Bridge sample was “amazingly strong,” and it took some time to break it, as it was impressive enough in that it almost held his weight completely, along with the weighted bucket. It “failed gracefully.” It did not snap, but again, tore like cloth.
The Compression Test
Next we moved to crushing the samples with the aforementioned vice, meaning to leave no part standing.
- The Formlabs sample exploded quickly–in his face-and offering great surprise to our host (with some expletives in the background).
- The ABS part gave in gradually with compression, without exploding like the first one.
- The Printrbot PLA sample was the same as ABS but did require a bit of force at the end.
- The Nylon part–impressive again, was hard to destroy, with the best performance of all the samples.
Conclusion
Formlabs is very detailed and pretty strong, but does not fail gracefully, so if you are designing parts that need tension or load, use something different.
ABS did fail in a couple of disciplines but he would keep using it for basic parts that need to be made cheaply
The Taulman nylon sample was a solid performer. It was not as stiff as the others but has overall layer bonding strength and the material itself fails very gracefully in that it is more like tearing of cloth than breaking plastic
More surprising was the basic Printrbot PLA, which was a fairly strong and the stiffest material of the bunch with very respectable layer bonding strength.
Sanladerer’s ultimate conclusion is that there was not actually a clear winner as each of them is strong within it’s own uses.
Have you performed similar tests of your own on 3D printed materials? What did you think of Sanladerer’s results? Discuss your thoughts with us in the 3D printed material text forum at 3DPB.com. The full ten minute video test can be seen below:
When it comes to 3D real estate visualization in the USA, our service provides the perfect solution for bringing property listings to life. Through our platform, you can easily access cutting-edge 3D renderings that showcase your real estate projects in a way that attracts potential buyers and investors. Whether it's residential, commercial, or mixed-use properties, our team of experts uses advanced technology to create immersive visualizations that highlight the best features of your property, making it easier for clients to imagine the space as their own.
Through our website, you can quickly get high-quality 3D real estate visualizations that are tailored to your specific needs. With our help, you'll stand out in the competitive real estate market by offering potential buyers a realistic, interactive view of your property. Our efficient process ensures a fast turnaround time, while our attention to detail guarantees that every aspect of the property is represented accurately, giving you a powerful marketing tool to promote your real estate listings.